IoT 導入により、進歩する予知保全
2020年08月06日(木)掲載
設備保全の抱える問題
製造業を中心とした第二次産業はもちろんのこと、運営に設備が不可欠である大型商業施設、研究施設、公共施設なども含めて、所有する設備の維持管理すなわち設備保全は、操業に関わる重要な課題になっています。
多くの企業や事業所で私が実際に目の当りにした「設備保全の問題」は、
例えば、
・設備の故障が多く、製造月度計画が達成されない場合もある。
・保全に関わる費用が多い。
・保全費用が年々増加している。
・設備導入後、時間の経過とともに老朽し、更新に大きな投資が必要になってきた。
・設備は無事動いているものの、メーカーのサポート終了宣言を受け更新を余儀なくされている。その費用が高額。
・後追いの保全になっており、計画的な保全、故障を未然に防ぐ保全に変えられない。
また、
・保全関係者の技術技能の育成が滞っており、社内に指導のできる人材がいないため、外注依存になりやすい。
・自社の保全活動が適正なやり方なのか、別のよいやり方があるのかも分からない。
などです。
これらから、「設備の安定稼働」と「保全費の削減」という二つの大きな課題が浮かび上がります。
設備の安定稼働は事業の継続のために不可欠であり、このためのコストが売上の5%を超える例もありましたが、ある程度の費用がかかることはやむを得ないとお考えの経営者の方も多くいらっしゃいます。
それに対して、設備の維持管理のIoT化を進め、機器装置の劣化状態を把握することで予防保全を行えば、安定稼働を妨げる設備故障と保全費の大幅な削減を実現することができると私は考えています。そして、実際にそのような事例を経験してきました。 設備の安定稼働と適正な保全費の実現は、保全活動の成果の両輪とも言えるものです。
このコラムでは、実例に基づきその両輪を達成する方法について解説いたします。
保全の指標
保全活動は、改善のスパイラルを継続して推し進めることが重要です。そのためには、まず、保全活動を数値として捉えること、それにより客観的な評価を行うことをお奨めします。
・安定稼働の指標:故障強度率
故障強度率は、設備が故障により発生し、復旧し設備を再稼働させるまでのロス時間の大きさを示します。
故障強度率(%)=100×故障による停止時間/設備稼働計画時間
となります。
他にも指標として、故障の起きる割合を示す、故障度数率という指標もありますが、まずは、故障強度率で考えましょう。
故障度数率(%)=100×故障停止回数の合計/設備稼働計画時間
・設備保全費
設備保全費とは、1年間に設備の維持管理のためにかかる費用の総額です。それには、以下の費用があります。
① 定期メンテナンス費:一定周期で行う整備や部品交換にかかる費用。
部品購入や外注費などに加えて、エレベーターや冷凍機、消防設備などのメンテナンス会社との定期保全契約も含みます。
② 突発対応費:設備の異常が発生し、復旧に要した費用。
③ 予備品購入費:ベアリングやガスケットなどの小物から予備ポンプなどの機器も含む費用。
④ 老朽更新費:老朽化やメーカーのサポート終了の対応として、計画的に行う老朽更新費用。稼働10年を過ぎると保全費に占める割合が大きくなってきます。
⑤ 人件費:設備保全に関わる自社要員の人件費。
⑥ 年間売上:会社、工場、製造ライン単位の年間生産売上または出荷金額。
指標として分析を行っていくために上記のような分類で生産ライン別・エリア別に集計することをお奨めします。
保全費比率=(①、②、③、④、⑤)/⑥
で捉えれば、自社内他工場や製造ライン間での比較も行うことができます。
まず指標は、設備強度率と設備保全費の二つで捉えることをお奨めします。
保全方法の変遷
保全の手法と考え方について説明します。
1) 事後保全:Breakdown Maintenance、略してBMと呼ばれています。
壊れたあとに修理する方法です。この事後保全には、2通りの考え方が存在します。
・緊急事後保全:Emergency Breakdown Maintenance: EBM
・計画事後保全:Planned Breakdown Maintenance: PBM
計画事後保全は、事後でも予備機への交換が容易であるなど、設備全体の稼働への影響が小さい場合に取られます。保全費用の面では、最小になる保全方法でもあります。
この他に、事後保全に対して予防保全があります。
2)予防保全:Preventive Maintenance、略してPMと呼ばれています。
壊れる前に保全をする方法です。この予防保全には4つの方法があります。
・時間基準保全:Time Based Maintenance、TBM
一定の時間ごとに部品の交換や整備を行う方法です。
・状態基準保全:Condition Based Maintenance、CBM
設備の劣化状態を把握しながら、適切なタイミングでメンテナンスを行う方法です。
・リスク基準保全:Risk Based Maintenance、RBM
予防保全を補完するための方法です。一つ毎の保全項目を安全・環境・品質の観点と故障時の停止時間や復旧費などでリスクを評価し、リスクの高いものに重点を置いて保全を行うという考え方です。
・状態&リスク基準保全:Condition& Risk Based Maintenance、CRM
現在のところ、最善の保全方法と評価しています。リスクの高いものをより注意しながら劣化状態を把握して保全を行う考え方です。状態基準保全CBMを基本としながらも、計画的事後保全PBMや時間基準保全TBMも取り入れながら、実行していきます。
これらの保全方法は、
事後保全BM⇒時間基準保全TBM⇒状態基準保全CBM ⇒状態&リスク基準保全CRM
と発展してきました。
時間基準保全TBMの問題点
時間基準保全(以下、TBM)は、整備の周期を決め、その周期が来たら部品交換等の整備を行う方法です。
その周期の決め方の例を2つ挙げます。
・エアコンプレッサー、大型冷凍機、エレベーターなどの装置
メーカー推奨のメンテナンス周期が、装置導入時に提示されます。多くのユーザーは、その推奨に従って整備を行います。
・ベアリングなどの劣化型部品
ベアリングの場合、メーカーより寿命計算式が提示されており、荷重や回転速度条件から寿命を算出できます。これに過去の実績を加えて評価し交換周期を決めます。
この手法においては、次の様々な状態が発生します。
TBMは、この周期を守ることが第一です。保全担当者は、メンテナンスのタイミングを守ることに注力します。整備作業は、限られた時間で行われる製造休止時に集中するため、外注することが多くなります。
交換された部品は、まだ使えるものが多くありますが、それでも故障は発生します。ベアリングを例にすると、劣化は荷重や回転速度以外にも周辺の温度や湿気、酸アルカリ等の雰囲気、潤滑の状態にも大きく影響を受けるためです。
TBMでは、部品レベルの劣化状態は把握していない場合が多く、整備周期前に突発的に故障することを防げません。
不意な故障は、重要な設備を部品以外の部分まで損傷してしまうことが多く、故障停止時間・復旧費用の両方がかさんでしまいます。
故障を発生させた部品は、さらに交換周期を短くせざるをえなくなります。
結果的に「保全費は、高額でかつ減少していかない。」「設備故障も多い。」という問題点が解消されません。
状態基準保全CBMの問題
状態基準保全(以下、CBM)は、設備の部品レベルでの劣化状態を把握することが必須の条件ですが、それが実現すれば、設備故障に至る前に劣化部品の交換を行うため、設備故障は減少します。そして、必要な部位のみ手を入れるので保全費も減少します。そうすると保全成果の両輪が回り始めますが、実現のハードルは高く、劣化状態のモニタリングが最重要となります。
まず、CBMを実行する保全担当者に必要なことは以下の2点です。
① 機器装置の劣化のメカニズムを知ること
必要な技術知識の例は、腐食、摩耗、疲労を始めとした損傷のメカニズムやベアリングや電装基板上の電子部品の劣化メカニズムです。劣化現象を知り、必要なモニタリング方法を検討することができることが必要です。
例えば、ベアリングの損傷現象は、初期衝撃波⇒振動加速度⇒振動速度⇒振幅、の順で出現しますが、現実的なセンシングとしては振動加速度の測定は効果がある、というような知識のあることです。
② モニタリングしたデータを判定し対応を決定できること
例えば、ベアリングの潤滑油の不純物測定結果を見て、油中に金属粉があった場合、潤滑油の交換は効果があるのかを判定できるレベルが必要です。
時間基準保全TBMは管理の保全であり、状態基準保全CBMは技術の保全と言われています。実現のためには、一気に管理の保全から技術の保全に舵を切らねばなりません。
高度経済成長期には、ほとんどの企業で時間基準保全TBMが実施されていたと思います。ところが、その時代でも状態基準保全CBMは存在していました。
実際にベテランの保全担当者の方々は、時間基準で整備を行いながらも、聴音器(医師の使う聴診器に似た)を肩にかけ、自分の担当エリアを毎日入念に巡回していたと思います。彼らベテランの五感が最大のセンサーでした。そして、五感で異常を感じると振動加速度計などセンサーを用いて測定を行っていました。まさに実践的な状態基準保全CBMです。
彼らは、時に先輩技術者から厳しく指導を受け、実践的に技術技能を積み重ねた結果、CBMの実行できるレベルに到達していました。
残念ながら、現在ではこのようなベテランの方々はほとんどいなくなってしまったように思います。もう、この時代には戻ることはできません。
IoT導入による設備保全の新しいやり方
キーワードは、IoTです。
高度な保全を実現するために設備保全最前線において、「設備の劣化をコントロール」する技術を有することは、もちろん必要不可欠です。その上でそれを補完しつつ実現可能なものにするのは、IoTであると私は考えています。
① センサーの活用
まず、かつてのベテランの五感に代わり、センサーを設置することを推奨します。例として、
・ベアリング、モーター:振動、温度、音、電流、電圧、回転数など
・クリーンルーム:塵埃、温度湿度、風量、ファン電流など
・制御盤内:温度、塵埃、ファン電流など
また、プロセス制御系より流量、流体圧、温度など運転状況をリンクしてください。
振動や温度センサーについては、無線によって、データ収集のできる比較的安価なものも販売されています。
また、防爆型のセンサーも増えてきました。これらは、IoTの一環として活用できるようになりました。
最新のシステムのAI技術で、これらによって収集した大量のデータの分析を行えば、ベテラン保全担当者の五感以上の判断を実現できるでしょう。
② 保全情報システム
現在、世の中に非常に多くの保全情報システムが出ています。このコラムでは、それらの個々の評価は省略しますが、最新のものには、IoTの情報統合を行い予知保全に活用できるものもあります。
選定にあたってのポイントは、状態基準保全の実施を考えたシステムであることです。
かつての保全情報システムは、時間基準保全TBMの忘れ防止機能を第一にしたものが多く、未だにその機能をメインとしたものがありますが、除外するべきであると私は思います。
・現場でデータを収集した端末(無線収集機、PADなど)との連携が可能で、収集したデータを集積し解析できること
・予備品や図面、社内他工場保全データの共有化ができること
・劣化判定の基準となるAI技術が盛り込まれていること
です。その上で付け加えれば、
・現場で使いこなせるもの
であることは、重要です。
CRMの奨め
CBMの実施には、技術のハードルがあることは説明しましたが、もうひとつハードルがあります。それは、設備コスト面です。
非常に数多くのセンサー、データ収集システム、ネットワーク、ビッグデータ解析可能なシステムの導入が必要になってきます。
初期の設備投資と後々の運用の面から、効率的で実現可能な状態基準保全の方法として「劣化状態&リスク基準保全:CRM」をお奨めします。この方法を説明します。
① リスク基準保全RBM:保全計画時に保全項目の1件別評価を行ないます。
保全機器全件対象でリスト化します。そして、1件毎に その機器が故障した際の「安全・環境・品質」に対する影響を5段階等で評価します。さらに予備品の有無、故障復旧時間、費用、設備稼働状況、予備機の有無などの観点で評価を行ないます。そして、その評価を基に保全手法を選定します。
予備あり、復旧も速やか、安全・環境・品質影響もないなど ⇒PBM計画的事後保全
重要機器であり、安全環境品質の影響も大きい。劣化状態の把握は可能⇒CBM劣化状態基準保全
重要機器であり、安全環境品質の影響も大きい。劣化状態の把握が困難⇒TBM時間基準保全
の様に機器によって保全方法の仕分けを行います。
すなわち、状態基準保全に舵をきったからといって、全ての機器をCBM化してセンサーを設置するわけでなく、ひとつの現場に複数の保全手法が混在することになります。これによって、CBMの設備投資のハードルを下げることもできます。
CRM劣化状態&リスク基準保全に舵を切った現場で、保全最前線の技術を高めながらCBMをさらに発展させ、設備強度率と保全費を50%以上削減したという実体験に基づき説明させていただきました。
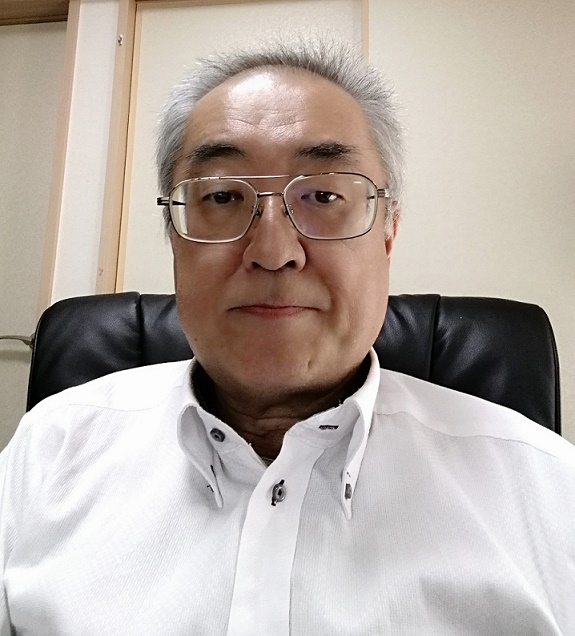
執筆者J.N氏
青山学院大学大学院機械工学科修士課程卒業後、化学業界の企業にて、プラントの計画、設計、施工、立上げから設備保全までを一貫して実施。退社後、生産現場を持つ企業のサポートを行うエンジニアリング会社を立上げ、設備と人の絡む領域の技術指導を中心に活動中。