IoT時代に変革が求められるPLM
2020年07月03日(金)掲載
「PLM」とは何か?
PLMはProduct Lifecycle Managementの略で、販売する製品のライフサイクルに関わる全ての情報を一元管理し、事業全体で効率化や品質の維持・向上に寄与するものです。PDM(Product Data Management)という言葉もありますが、PLMとの線引きは少々曖昧です。なぜかというとPLMのようなPDMやその逆も存在するからです。
私自身の理解は、最初に設計業務の効率化、設計・製品情報の一元管理のためのPDMシステムが誕生し、その後機能拡張をしたものがPLMシステムだと認識しています。PLM/PDMの”M”はマネジメントの”M”ですから、そもそも考え方や手法であり人それぞれ異なるものですが、PLM/PDMシステムは、システム(道具)なので、マネジメントを支援するものです。ここで記すPLMは主にPLMシステムだと思ってください。
製品情報にはどのような種類があるかというと、製品名やジョブの名前、それに紐づく設計図面、部品構成表(以下BOM:Bill of Material)、納入先の国別に必要な手続きや規定文書など、場合によっては製造に関する工程情報や原価情報などがあります。導入・運用する部門が設計部門なので、設計業務効率の改善が目的であると思っている方も多いかもしれません。間違いではありませんが本来期待すべき効果は別のところにあります。冒頭に記したように、会社全体または事業全体で大きな効果をもたらすものなのです。さてそれはどのようなことでしょうか。
IoT時代の到来でその重要性が再認識されている「PLM」とは
「何をいまさらPLMだ」と思っている方も多いかもしれませんし、「そうそうPLMが大事なのだよ」と思う方もいるでしょう。大きな会社・事業になるほど、担当されている方の中には、IoT等と繋げて重要性を理解してくれる人が少なくて悩んでいる方も多いのではないでしょうか。製造業において、IoTは工場で実施中、PLMは設計で導入済みという会社も少なくないと思いますが、両部門がデータ活用という視点でどれだけ連携しているかで両施策の効果が全く変わります。
IoTの推進で製造現場における様々な情報がデジタル化され「見える化」されつつあります。各部門の業務に必要な情報が人を介さず、見たい時に見たいように見ることができる時代です。設計通り製造できたのか、加工精度はどうだったのか、実際原価はいくらだったのかなど、製造部門や品質部門、保守サービス部門で何かをキーに情報を探せばすぐにリアルタイムの情報が手元に現れる時代です。人が確認や分析をしなくてもAI技術で予知・予防もできる場合もあります。製造IoTにおけるデータ活用は、設計情報が活用可能な状態で準備されていれば、今までできなかったことや時間がかかっていたことをたくさん解決できます。
すなわち、IoTの可能性、ポテンシャルを大いに高めるのがPLMなのです。
設計とものづくりとを繋ぐBOMの重要性
PLMで管理する最も重要な情報の一つにBOMがあり、これは「部品構成表」を指します。使用する部品が定義されているだけであると思うかもしれませんが、上手く使うことで部門間の共通言語として大活躍するのがBOMです。設計が作るBOMsである「設計BOM(E-BOM=Engineering BOM)」に対して、部品や材料を調達するための「調達BOM(P-BOM=Procurement BOM)」や、製造するための情報を付加した「製造BOM(M-BOM=Manufacturing BOM)」という考え方も一般的で、業務連携をする上で大変重要な役割を持っています。
製造で使用するBOMには工程ごとの加工時間や倉庫までの物流リードタイムまで設定できるものもあります。定義されている部品に対して原価情報を定義すると、そのBOMを使って見積回答できる可能性もあります。使い方次第で設計情報が製造やサプライチェーンのマスター情報として機能する活用事例は多く存在し、そのマスターをIoTで自動計算、自動設定することも可能なのです 。
製品のライフサイクル上の段階別ポイント
さらに理解を深めるため、「製品ライフサイクル」について補足をしておきたいと思います。量産品と個別受注品では管理ポイントが異なりますので、異なる部分については明示して説明します。
(1) 開発段階
商品企画や顧客が求める機能を実現するだけではなく、高品質に安く早く作れる設計が求められます。全く新規のものは試作と評価を繰り返し、量産品の場合は安定して迅速に大量に製造するために生産技術部門と連携して設計を完成させます。設計過程で仕様を確定させていく場合もありますが、確定を待っていると部品の手配や製造の準備が間に合わず、納期や発売時期に影響を及ぼしてしまうケースもあります。
PLMの役割は、早い段階から設計情報を共有して、同時並行に求められる要求を解決していくことです。例えば設計の早期段階で、3D図面を製造部門が確認して製造上の問題点や疑問点を提示すること、品質部門が品質のチェックを行うこと、資材部門が材料調達面でのコストや調達容易性を評価することなどがあります。これはコンカレントエンジニアリングという手法が当てはまります。
個別受注品はあらかじめ売価が決まっている場合が多く、原価管理が非常に重要です。開発段階でどれだけ原価(見込原価)を抑えられるかは簡単ではない課題です。PLMに部品や工程の情報が正確に設定されていると、精度の高い見積と販売価格の提示が可能になり、より確実に利益を確保することができます。
(2) 生産段階
量産品の生産はライフサイクルが数年(場合によっては十年以上も)あり、その間生産計画策定、MPR(資材所要量計算)を繰り返します。重要なポイントは生産計画(数量)とBOMの管理です。需要の変動に応じて生産計画の増減を実施しますが、製品在庫や部品在庫が回収(売上)不能な在庫にならないように管理をしなければなりません。BOMの活用として、部品や材料のサプライヤー変更(マルチベンダー対応含む)による部品番号の変更や、保有在庫を元にした使用部品の変更期日、仕向け先別の使用部品のコントロールなどがあげられます。
個別受注品の生産開始から完成・出荷(納入)までの段階で注意すべきポイントは原価管理です。特に生産リードタイムの長い製品は、その間に部品・材料の価格変更、工数の増加、仕様の変更や納期の変更で製造原価や物流費が見込原価よりも上がってしまう場合があります。顧客の都合で変わる場合は売価を変えていただく調整ができればよいですが、できない場合もあり要注意です。
従ってPLMで管理されている標準原価や見込原価と、IoTでリアルタイムに取得できる情報から算出する実際原価を比べて、最終的に利益がでるようなコントロールが期待できます。
(3) 生産終息期(EOL: End of Life)
量産品において、後継機種への移行または生産・販売終了を見据えたコントロールをしなければなりません。対象機種にしか使用できないユニークな部品が残って廃棄ロスになる場合や、完成品の在庫が売り切れない場合は大きなロスになるため、極力売り切るための計画策定が求められます。それが困難で倉庫に保管したまま回収困難な部品・製品は、資金回収ができないばかりか、時間が経過するほど保管費用が原価(コスト)として積み上がり、場合によっては品質にも影響します。従ってある時点で廃棄という判断が必要で、その判断を容易に助けるのがPLMとIoTでもあります。製品別の在庫鮮度や原価がリアルタイムで把握できれば、都度人が集計や分析を行うことなく、ダッシュボード機能等と組み合わせてアラート発信する仕組みは容易に構築できます。
(4) サービス・サポート(フィールド)
顧客が使用している製品にトラブル等があった場合、サービス・サポート部門が顧客からその連絡を受け、現地確認や返品受付、修理・交換等の対応を行います。その間顧客は待たなければなりませんし、出張費用や修理・交換に関する費用も発生します。
最近ではIoTで遠隔監視を行い、消耗品の交換を事前に促すことや、異常を察知してアラート出すことも可能になっています。PLMで管理されている製品の情報を元にして、自社にも顧客にもロスがでない仕組みの構築が可能です。遠隔監視ができない製品に関しても、製造IoTで製造工程の履歴や使用した部品、品質データが取得されていれば、ロット不良を早期に見つけて迅速なサポートにつながるかもしれません。
IoTやAI技術を活用した次世代ものづくりにおけるPLMの役割
IoT推進により、取得したデータからAI技術を使って、製造設備の故障予知や品質管理を行っている事例が数多くみられるようになりました。日本でAIの実用化が進み始めてきた当初は製造業の事例は少なかったのですが、近年は製造業の事例が増えています。しかしながら、事業全体でデータ活用が進んでいるという事例はまだ多くありません。設備や工程といった閉じた世界で活用されていることが多く、それ自体は非常に有意義なことですが、IoTやAIの可能性を考えると、まだこれから発展の余地はたくさんあり、鍵を握るのかPLMではないでしょうか。
ものづくりにおけるデータ活用を考えると、製造工程で取得したデータのみを活用するのではなく、設計情報、製品情報などと合わせてデータ活用をすることで、今とは違った製造品質管理や原価管理、在庫管理も可能になるはずです。
複雑な組立作業や設備のメンテナンスにおいて、作業者がスマートグラスを装着してARで見たい設計情報や作業手順を3D(三次元)で分かりやすく表示することがすでに可能な時代です。熟練した作業者の後継者がいないという問題の解決手法としても注目されています。
PLM導入時の現場のリアルな課題
では、すぐにPLMを導入しようと思っても、実は簡単にいくものではありません。
1点目はシステムの選択です。PLMが登場したばかりの時代は、数千万円~数億円と非常に高価なものが主流でしたが、近年安価なPLMが多く登場し、無償のPLMも登場しています。安価なものは機能が限定されている場合が多く、カスタマイズや追加オプションで導入コストがかかる場合もあります。またシステムの性質上導入すれば誰でも直ぐに使えるものではなく、導入コンサルティングが必要な場合はそのコストも考慮しなければなりません。対象事業の規模や対象製品、品種数や材料、部品の種類、使用しているCADシステムとの相性、求める機能の範囲、関連システムとのインターフェース有無や容易性を含め、会社・事業にマッチしたPLMシステムの選択をするのは難しい課題です。
PLMシステムは道具なので使い方次第ではありますが、オーバースペックなものや、逆に機能不足にならないように注意する必要もあります。対象事業が販売する商品がシンプルな設計に見えて意外と複雑なバリエーションを持っている場合もあります。また、社内で選定する場合はPLM製品のポテンシャル以外にセールスマンの対応や選定者の嗜好で選定される場合もあるため、客観的な評価をシステム選定プロセスに入れることをお勧めします。
2点目の課題は新しいシステムへの移行です。マスターの設定等の準備、過去の設計成果物の移行、場合によっては古いシステムと並行で運用していく場合もあります。その場合は対象部門の負荷が非常に大きくなるということを覚悟して、支援リソースの準備などを計画するべきです。
3点目は、運用上の組織間の責任分担です。設計部門任せにならないよう、用途に応じて関係部門がマスターメンテナンスや情報の精度に対して責任持つルール決めを事前に行うことも重要なポイントです。それによって情報の相互活用による相乗効果を得ることができると考えます。
PLM導入と3D設計の重要性
最後に重要な点を付け加えておきます。それは3D設計を主にするか、それとも2D(2次元)が正で3Dは活用場面で使う(または使わない)レベルにするのか、ということです。顧客や材料・部品サプライヤーとの図面とやりとり等の関係、CADオペレータのスキルの問題もあり、特に日本の多くの製造業は2D主体から脱することができていません。
海外では3Dのみで完結している企業が多いため、ドイツのIndustry4.0や米国や中国の先進企業の取り組みにおいて、デジタルツインの構築も進んでおり、デジタルツインを活用した事前のシミュレーションにより後戻りの少ない短期間での設計開発や、多品種においても全自動に近い製造が実現しつつあります。日本企業が直面している人材不足や、それによるノウハウの継承問題などを解決する手段として、3D設計主体に切り替えることは非常に有効でしよう。
日本のものづくりはまだ世界で戦える
IoTもPLMも日本は後進国です。情報システムを道具として活用することが苦手なのか、AI含むデータ活用が進まないからなのか、はたまた組織間連携が苦手なのか、様々な理由があると思います。
一方で日本のモノづくりは今でも世界で評価されています。特に日本品質の評価が高いことは承知の事実です。ものづくりだから製造品質であると思いがちですが、品質・コストの大半は設計で決まるとも言われています。量産品であれば量産する生産技術に耐えうる設計を製造と両輪で作ることで日本品質が実現しています。個別受注品も設計と製造が深いコミュニケーションで高品質を実現しています。今後はその品質をPLM活用で形式知化し、早く正確に行うことに注力すべきではないでしょうか。
日本のものづくりの優位性、品質に対するこだわりを3D設計主体としたPLMの運用に乗せることができたら、日本の製造業はまだまだ世界で戦えると信じています。
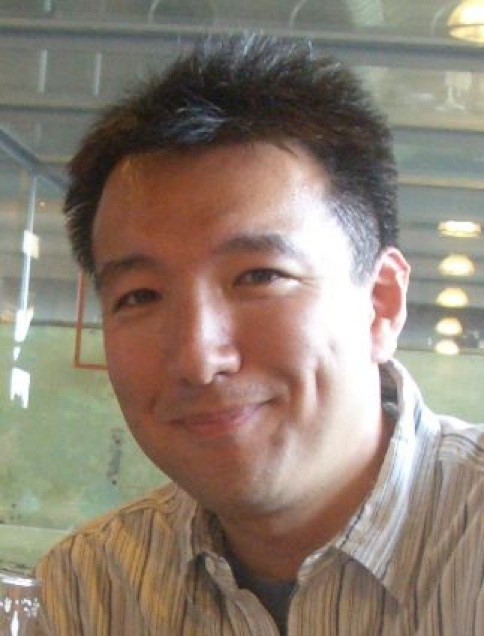
執筆者K.S氏
大学卒業後、エレクトロニクス業界の大手企業に入社し、生産技術部門勤務。
グローバル売上数千億円規模のデジタルプロダクト事業にてSCM導入とマスカスタマイゼーションを効率的に実現するPLMの活用を牽引。IT外資系企業や物流業界の企業を経て、製造業にてCDOとしてIoTや全社デジタル化を推進。