コロナ禍からの復活のためのスマートファクトリー実現に向けて|課題・メリットも
2020年11月11日(水)掲載
スマートファクトリーという言葉をご存知でしょうか。ドイツ政府が提唱する先進的な工場のことです。デジタル化を通して生産性を向上し、業務プロセスを簡略化することです。
私が“スマートファクトリー”という言葉を初めて聞いたのは2010年のことです。仕事でお付き合いのある方から一冊の本を勧められました。当時私は物流会社に所属していたので、さらっと読み流した程度でピンとこなかったのですが、読み返すとまさに今仕事で進めていることが書いてありました。
印象に残っているのは、全ての設備の情報を接続・連携してリアルタイムに状況がわかると、「工場のマネジメントが劇的に変わる」という内容です。
スマートファクトリーとは?
“スマートファクトリー”は高度な自動化
スマートファクトリーと自動化は同義ではありませんが、近いものと解釈できます。組立や加工プロセスの自動化はロボティクス技術で進んでいますし、間接業務もRPAの普及等で自動化が進んでいますが、この自動化にインテリジェンスの要素が加わらないとスマート化とは言えないでしょう。近年は高度で複雑な処理等を加え、今まで人間が実施するのが当たり前だったことまでを自動化してしまうのがスマート化と考えます。
例えば材料加工や組立工程の場合、自動化されれば設備の状態は自動で取得できます、すると稼働日報の作成や稼働率の集計や分析など生産性改善のための様々な管理業務も自動化することができます。自動化が困難な組立・加工プロセスについても、センサーなどで多くのデータが取得でき、そのデータを活用することで管理業務も自動化されていきます。人の仕事をどんどん自動化し、人は人しかできない部分を強化するのがスマートファクトリーの本質だと考えます。とりわけ日本の場合は「人が保有している過去からのモノづくりのノウハウ」を極力デジタル化、AI化、すなわち”スマート”な自動化にすべきではないでしょうか。
日本が得意としてきた人による管理業務の自動化、それこそ工場のマネジメントが劇的に変わるということです。さらに例をあげます。
(1)生産性・進捗
従来は製造現場に進捗掲示板があり進捗をわかりやすく表示してタイムリーに遅れを把握してアクションに繋げる役割を果たしていました。今後は製造現場にいなくても事務所や外出先でも進捗がわかるようになります。また遅れに対して自動で対策・対応を提案することも可能になります。
(2)品質管理
従来は不良が発生した後の対応になることが多いですが、今後はタイムリーに品質データが把握でき、アラートをメールやSNSで発信したり自動で設備やラインを停止・復旧したり、さらにはデータを蓄積して学習することで予知することがあたりまえのように実装されていきます。
(3)在庫管理
在庫もリアルタイムで変わります。人が数えたり入力したりするのではなく、また日次や月次で在庫分析をすることもなく、今後は自動で在庫数を把握でき、基準の在庫を超えたら自動で計画を減らしたり、在庫が無くなってきたら計画を増やしたり、部品を自動発注したりすることがあたりまえのようになっていくでしょう。
(4)原価管理
今でも正しい実際原価を詳細レベルで把握できている会社は少ないのではないでしょうか。今後は設備や人が何をどのくらい時間をかけたのかデータが取得できるため、マスターデータを正しく登録しておけば、製品別に実際に極めて近い原価を把握することが可能です。これを元に標準原価を設定して、製造コストを削減することや、売上・利益の目標設定も明確にすることが可能です。
(5)予知保全
従来故障や不良が起こってから対応していたことが、データの蓄積と分析・学習により、故障や不良を事前に予知することが可能になってきました。振動センサーや熱センサー、カメラなどの画像等、製造現場の状況を人間の五感の代わりに伝え、将来の予測をしてくれる、まさにスマート化の代表事例と言えるでしょう。
これら多目的かつ複雑できめ細かい管理こそ日本の強みではないでしょうか。それを新しい技術を使ってスマートファクトリーにすることが復活・逆転の鍵だと考えます。
現状の日本のスマートファクトリーの問題点・課題
日本の製造業は苦境に立っている
日本はこの分野で大きく後れをとってしまい、コロナ禍でそれが大きく露呈しています。工業製品の供給は中国が主体、アメリカはGAFAに代表されるIoT先進国で、ドイツはIndustry4.0を掲げ高い労働生産性と高付加価値な製造で確固たる地位を築いています。自動車産業に代表されるモノづくり大国日本はかつての栄光を取り戻せるのでしょうか。
自動化技術において日本の製造業は欧米や中国に大きく後れを取ってしまったことは違いありません。日本企業は中国に生産をシフトする中、今までの日本のものづくりに拘りつつコストダウン競争に巻き込まれ、情報システム投資が不十分かつ人材も不足している状況のため、なかなか先手を打つことができていないのが実情です。
デジタル化への反発がある
そしていつの時代も「変える」「変わる」ことへの不安や反対が多くの関係者からあがります。そろばんで計算していた時代は電卓を使うと計算力が落ちるという懸念と反発、手書きの書類をワープロで作成すると漢字が書けなくなる懸念と反発、電子メールを使いだすとコミュニケーションが疎かになるという懸念と反発と、便利な道具が登場するたびに、弊害や副作用を訴えて反対する人がいるものです。しかし世の中は便利なものを使う宿命にあります。江戸時代に比べると移動するときは自動車や鉄道、飛行機を使いますし、家電製品を持っていない人もいないでしょう。反発する人たちも日常生活ではデジタル化された便利な道具に囲まれているはずですね。
失われてしまうかもしれない大事なことは別の方法で補うことをお勧めします。そうしないと新しい便利な道具を使いこなす会社(特に海外勢)にどんどん差をつけられてしまいます。生活が便利になるのに会社の仕事はいつまでも変わらないわけは無いのです。
反対派には冷静に説得する準備を行って挑みましょう。特に年配の「私はアナログ人間だ」とデジタル化にネガティブな管理職には「若い社員の未来のため」と言えば理解していただけるかもしれません。
スモールスタートへの過剰な対策がされている
デジタル化やIoT関連の宣伝文句に、「まずはスモールスタートから」 という文句をよく見ます。
スモールスタートからというのに反対はありません。スコープを絞って安く早く結果を確認しながら進めるのは鉄則と言っても過言ではないでしょう。データを取得する仕組みとそれを活用するシステムがセットになってフルパッケージを全て賄ってくれる。そしてとても安価。そこに飛びつく気持ちもよくわかります。しかし「安物買いの銭失い」になりかねないケースもあります。また、スモールスタートで終わってしまうケースも多いようです。あくまでもスタートなのでその先何をどこまでやろうとするのかによってスターの仕方もよく考えなければなりません。
例えば稼働情報を取得してリアルタイムに稼働率や設備の停止を見える化できるパッケージがあります。簡単に設置できて、事務所のパソコンで綺麗な稼働率のグラフがすぐにみられるようになりました。スモールスタート成功です。
次に何をするかというと、2つのパターンが考えられます。
(1)他の設備に同じ仕組みを設置(展開)しよう
(2)稼働情報以外の生産個数や品質情報(計測値)も取得しよう
前者(1)の場合、機器を追加していけば容易に展開できます。しかし(2)の場合、スモールスタートで提供されたデータ活用のシステムは数量や品質情報を活用する機能が無い場合が多いです。カスタマイズにお金をかけるか、別のシステムを作らないといけません。最初は安く構築できたのにすぐに追加投資がかかってしまいます。
さらに(2)で述べた情報・目的以外にも、電流計や振動センサー、熱センサー、赤外線センサーなどを後付け外付けして予知・予防保全、エネルギーコストの見える化など、あらゆる情報の活用が考えられます。
IoTとは人間の五感のようにセンサーを張り巡らし、情報をネットワークに繋げてデジタルツインを構築してそのデータをAIなど活用してインテリジェンス化することが期待されています。まさにスマートファクトリーの姿ではないでしょうか。
スモールスタートのその先にビジョンが描かれていないと、スモールスタートの意味が薄れてしまうかもしれません。
スマートファクトリーを実現する製造業にとってのメリットや価値
では、スマートファクトリーを実現することによって得られるメリットや価値は何なのでしょうか。
見える化ができる
一番大きな効果は「見える化」ができることです。稼働状況や製造実績をデータ化し、それらが可視化した工場を目指すとき、その指標は全てデータ化、すなわち数値化されます。によって、データを分析したり、数字で判断したりすることによって、現状の分析が可能になります。
例えば、工場のどこかで不具合が起こった時もそれを管理しやすくなり、ミス防止やリスク管理に繋がります。適切な現場判断ができるだけではなく、経営判断にも時には効果的です。製造業では、属人的なタスクが少しでもあると、感覚的な判断が重視されてしまう傾向にあります。もちろん、感覚的な判断は軽視すべきものではないですが、そこにデータの裏付けができた時、より確実性の高いものになります。
工場同士が繋がることができる
各拠点の工場間や拠点間で情報を連携することができます。10年以上前の工場では、この情報共有システムができるなんて想像できる人はすごく少なかったでしょう。
工場同士で連携した情報を定量的に比較することが可能になります。そうすると、リソースの横展開や、生産計画などの経営判断を早急に行うことが可能になります。
スマートファクトリーへの展望
では、スマートファクトリー実現に向けて、どのようなステップを踏んでいけばいいのか解説していきます。
スマート化するためにはデジタル化することが改革のステップ
一足飛びにスマート化にはなりません。まずは製造現場の人に依存しない「見える化」です。先に述べたスモールスタートの仕方に注意して将来の構想を会社内、メンバー間で共有してそのイメージの第一歩として進めましょう。決して最初の一歩で効果に拘らないことも大事だと思っています。見える化は手段であって見える化された後にどうするかが重要だからです。
データ活用は現状打破のためにすべきこと
スマートファクトリーは従来人間が五感で感じていた現場の情報がデジタル化される前提で成り立つものと考えます。デジタル化ができれば次はそのデータ活用(脳と手足の構築)を進めなければなりません。その活用こそやり方によっては人間以下にも以上にもなります。AIシステムを構築したとしても5歳くらいの知能にも熟練したベテランの知能にもなりえるということです。様々なデータの相関を導き出したり、短時間で大量の計算をしたりと人間ではできない処理で驚くべき結果を出す可能性を秘めています。そこにたどりつけるかが大きなポイントとなるでしょう。
デジタルツイン
人に依存しないスマート化された工場(=スマートファクトリー)は、デジタルの複製(コピー)を持っているようなものです。何かあったとき、例えば国と国の問題でサプライチェーンを大きく変更しなければならない場合、迅速に変更を行うことも可能です。どこ国で製造しようとも生産性や品質を損なわずに再現できる可能性も秘めています。新しい工場を立ち上げる時に人の育成を最小限にするために既存の工場ごとデータ保存されていると考えて良いでしょう。
人気の関連コラムを読む
まとめ
工場のマネジメントが劇的に変わるのが“スマートファクトリー”であると述べてきました。今まで翌日に報告を聞いてからした把握できなかったことが、リアルタイムに把握できるので、タイムリーに把握できアクションが早くなります。月締めでデータをまとめて、月次報告で対策していたことが日次で可能になります。人が見落としたり、間違えたりする要素が少なくなり、生産性や品質が格段によくなるでしょう。他の国とは異なるレベルのものづくりへの気概、品質へのこだわりや生産性改善のノウハウなど日本特有の内容には必ずアドバンテージがあります。日本ならではのモノづくりとデジタル化が融合した時に、新しい日本のスマートファクトリーの出現が期待されます。
未来のあるべき姿のイメージを描きながらデジタル化を進めデータ活用のアイデアを具現化していくと、いつの間にか他国にはない圧倒的な“スマートファクトリー”になっているのかもしれません。
人気の関連コラムを読む
コロナ禍でオンライン化やリモートワークが進み、製造業にとっては逆風が吹いていました。ロックダウンや三密などを通して、業務に弊害が出ていた企業がほとんどだと思います。しかし、多くの企業においてDX化が劇的に進んだ今、変化の年にもなっています。ここで、変化の波に乗り、経営戦略を正しく立て直していくことが重要です。HiPro Bizでは、経営プロ人材を紹介しています。自社の課題に合わせた最適なプロ人材を選び、スポットで依頼をしたり、社外取締役として長期的に支援をしてもらったり、自社にとって最適な形で提携できるのが大きなメリットです。ぜひまずはご相談ください。
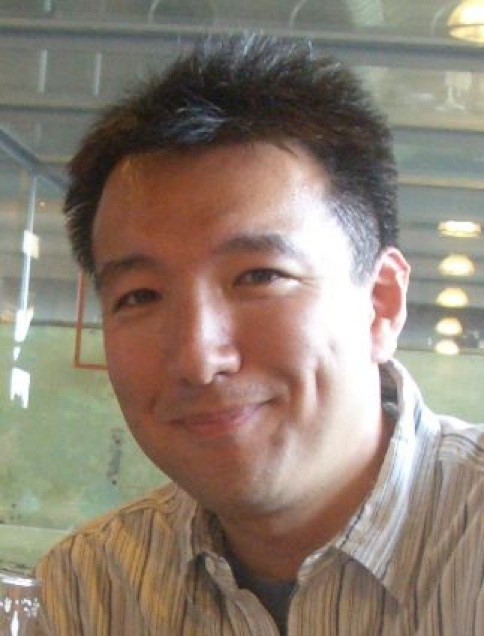
執筆者K.S
早稲田大学理工学部卒業後、総合電機メーカーに入社し生産技術部門勤務。グローバル売上数千億円規模のデジタルプロダクト事業にてサプライチェーンマネジメント導入とマスカスタマイゼーションを効率的に実現するPLMの活用を牽引した。現在金属加工メーカーにてCDOとしてIoTや全社デジタル化を推進中。