製造業における5S
2020年07月03日(金)掲載
製造業において多くの工場や倉庫などで掲げている5Sですが、実は様々な業種・業態において役立つものだと思います。なぜならば、5Sとは企業活動の中に存在する「ムダ」を無くすことで、コストを減らし安定して良い品質・サービスを提供し続けることに繋がるからです。うまく活用すれば、強固な利益体質になる手法なので、多くの方に興味を持っていただきたいと思います。
人に例えると、毎日の食事、睡眠、運動、学習について自分に合った規則を習慣とし、筋肉質で病気になりにくい身体をつくること、それを維持し続けることです。決して即効性のある薬のようなものではないことを念頭に読んでいただけると幸いです。
5Sとは
はじめに5Sの定義を確認しておきましょう。十分理解している方もたくさんいると思いますが、実際よくわからないという方のために一般的なわかりやすい表現で定義を記します。
<整理(せいり:Seiri)>必要なものと不要なものを区分して不要なものを捨てること
<整頓(せいとん:Seiton)>使いやすく並べること
<清掃(せいそう:Seisou)>掃除を行いきれい(クリーン)にすること
<清潔(せいけつ:Seiketsu)>整理・整頓・清掃が実現・維持された状態
<躾(しつけ:Shitsuke)>清潔を維持できるよう習慣づけること
言葉にすると特別なことではなく難しくないことです。実生活で実践できている方も多いでしょう。ではなぜ製造業において多くの会社がモノづくりの基本として取り組んでいるのでしょう。そして取り組んだ企業が必ずしも成果に繋がっているわけでもなく、うまくいかないケースもよく聞きます。それ故、本当に5Sに注力すべきなのかと悩んでいる方も多いのではないでしょうか。今回はいくつかの事例や私の考えを紹介して皆さんの今後の指針にしていただけたらと思います。
5Sの解釈
定義は簡単ですが「正しい解釈はこうです」という唯一の答えがないのが5Sといえます。例えば武道などでも解釈によって流派がたくさん分かれますが、それぞれ自分に合ったものを選ぶのではないでしょうか。5Sも対象となる事業や工場にどのように適用するか、何に重きを置くかも多少異なってくるため、いざ取り組もうと考えた時に、それぞれの解釈が生まれてくると思います。
「わが社の5Sはこれでいこう!」「わが工場の5Sはこうしよう!」というトップの意志を言葉にし、行動にして推進することが大事です。例えば、まず2S(整理・整頓)を重点的に行うことや安全(Safety)などを加えた6Sや7Sというのも聞いたことがあります。トップの意志が反映されていれば良いと思いますが、元の定義を外しすぎた独自路線はお勧めしません。参考書や資料は数多くあるので、共感したものに合わせるのもよい方法の一つです。
例えばこんな5Sはいかがでしょうか・・・解釈例
それではまず、私の考える5Sの解釈を紹介します。冒頭に紹介した定義も残しています。
<整理> 必要なものと不要なものを区分して不要なものを捨てること
作業場所に存在するものが今直ちに必要なモノなのかを点検して、今必要のないものは極力置かないようにすることを徹底する。作業現場または作業者に提供されるのは必要な情報のみ、必要なタイミングで提供するようにする作業者の動作は必要最低限の動きで作業ができているか点検し、歩く、屈む、手を伸ばすなど一つ一つの動きは本当に必要な動作なのか、作業の開始から終了まで安定して同じスペードと正確さで作業ができる方法なのかを常に確認を行い、ムリな動作やムダな動作を無くすようにする。
<整頓> 使いやすく並べること
誰でもすぐにわかるような置き方、何がどこにあるかわかる状態、使いやすい状態にする。いつも違う場所に置かれていたり、左右逆であったり、まっすぐもしくは斜めであったりすると、使う人の作業にムラがでる。わかるひとにだけわかる置き方であると習熟していない作業者は慣れるのに時間がかかる。誰が作業しても作業の速さ正確さがかわらない置き方が理想。
<清掃> 掃除を行いきれい(クリーン)な状態にすること
単に掃除を行うだけではなく、汚れの原因を追究して掃除の時間を減らしたり、汚れの原因を無くしたりすることまでを含む。自ら掃除を行うことで自らが汚れを発生させることも無くせる。自分で掃除するトイレはきれいに使うはずですし、自分で汚したものは自分で掃除する習慣にもなる。クリーンな状態の製造現場ではそれがつくるモノ(製品)の品質にもつながる。
<清潔> 整理・整頓・清掃が実現・維持された状態
整理・整頓・清掃は、やめてしまうとやがて元のムリ・ムダ・ムラのある職場に戻ってしまう。常にムリ・ムラ・ムダの無い状態を維持することは大変難しく、維持するための仕組み作りをすることが必要。例えば、5Sパトロールや5Sのコンクールなど常に5Sを意識した活動があると緊張感のある職場が維持される。
<躾(しつけ)> 清潔を維持できるよう習慣づけること
上から押さえつけるような厳しい指導方法ではなく、5Sの基本や職場のルールをわかりやすく教え、全員がただしく理解することを第一とする。なぜ整理・整頓・清掃をする必要があるのか、そうしなくても作業は問題なくできるという意見に対しても納得できる答えを用意し、腑に落ちるまで理解させることが大切。例えば社内全員参加の教育体制を整備する、定期的に現場を巡回しあって指摘や意見交換を繰り返し行う、小集団活動の中でリーダが教えながら改善することも有効。
定着しないケースやその理由
5Sがうまくいかない、または何度行っても定着せずに元のレベルに戻ってしまうということをよく耳にします。
トップダウンで進めることが重要ですが、製造現場のメンバーがなぜ5Sをやらなければならないのか、5Sで何が良くなるのかを正確に理解していない場合はうまくいきません。会社の方針であるから、会社の決まりだから、上司の指示だからなどの理由で行っている場合は、そのような状態そのものが5Sではありません。思い当たる5S阻害要因をいくつかリストアップしてみました。
(1) 納期に追われて加工・組立作業で手一杯
(2) 納期、安全、品質の指示が数多くあって作業者は優先度がわからない
(3) 作業は一部請負業者に依頼しているため一緒に活動できない
(4) 何から始めてよいか手順がわからない
(5) 現場まかせになっている
(6) 活動を継続しても効果が見えにくい
製造現場も労働者が多様化しており、すぐにやめてしまう人もいる中で、5Sの中身を常に理解させ続けることは大変難しいことかもしれません。活動時間そのものがムダではないかという気持ちも理解できます。そのような壁を乗り越えていくうちに、気が付かない間に製造現場は洗練されていきます。そのためにも正しい理解と意志のこもった解釈、強力なトップダウンによる全員参加の活動にしていかなければなりません。
ムリ・ムダが無く安全な職場
私は今まで様々な製造形態の工場を見てきたためか、製造現場によっては「パッと見た」だけで製造のレベルがわかるようになってきました。この一瞬見て感じたことが意外と肝なのです。その話は後述することにして、過去に経験した5Sにまつわるお話を紹介します。
ある製造現場で労働災害が発生しました。作業者が止まってしまった設備を動かすためにその設備に手を入れたところ、別の動いている設備に干渉して軽い怪我をしてしまいました。 対策としてエリアセンサーを設置し、設備担当が設備の修理・改善を直ちに行うことなどの対策を施しました。ところが、しばらくして違う災害が発生しました。重たいものを載せた台車が動かなくなり、力を入れたら足を轢いてしまい怪我をしました。その際も台車への改善を主体に対策を講じています。2つの災害に共通していることは何でしょうか。それは、作業標準にはない(または作業として定義もされていない)「ムリ」な作業をしているということです。その災害の直因に対して都度対策を講じるだけではなく、常日頃から「ムリな作業をしない」ということが徹底されていれば、災害は防げたのではないでしょうか。私の考えは、5Sをしっかり行っていれば製造現場の安全は担保されるということです。
もう一つ、これは海外工場の話を紹介します。ある工場を訪問して製造現場を一通り見学させていただいた後で、私は案内してくれた方に「この工場は労働災害が多くないですか?」と聞きました。担当の方は「はい、多くて困っています。でもなぜわかるのですか?」 と答えました。なぜわかったのかというと、日本に比べて人の入れ替わりが多い海外の工場で、通路が曲がりくねってわかりにくく、置き場所ではないところに工具や部品が置いてあるなど、見学するにも少々危ない様子でした。
「ものを避ける」「歩くときに注意する」というムダな動作を知らず知らずに放置してしまっていたようです。慣れた作業者はそれが当たり前として対処できますが、新しく入った人は知らずに怪我をすることもあるでしょう。慣れた人でも慌てている時、疲れているときはぶつけたりつまずいたりする可能性があります。
そもそも安全は作業者自身のために確保されるべきことです。作業者を大事に思うのであれば、なおさら会社・工場でムリ・ムダ・ムラの無い安全な職場にすべきでしょう。そして、働いている人を大事にするということは、働いている人が作るものを大事にすること=高品質にも繋がります。まさに日本の製造業の本質でなないでしょうか。
良い製造現場の事例
私が見た中で素晴らしいと思った事例を断片的ですが紹介したいと思います。
それぞれの事例が解説を行うとそれなりに長い文章になりますので、今回は解説を省きます。
(1) 見渡す限り目に入る作業者の全員がテキパキと作業をしている
(2) 掲示物が常に最新の情報である
(3) 製造現場にあるものが情報発信をしている(表示や札)
(4) 通路がまっすぐで広く、垂直平行が徹底されている
(5) 作業者が誇らしげに説明し、私の職場という高い意識で改善を継続している
(6) 作業場、置き場、通路の3区分管理が徹底されている
(7) 改善活動に関しては管理レス状態
(8) トイレがきれい
まだ他にもありますが、5Sをするとなぜそのようになるのか、このような事例がどのような効果につながるのか、ここではあえて答えを書きませんので、考えてみていただけると幸いです。
新しい時代の5S
自動化やIoT、AI技術の実用化が進んでいますが、5Sはもう古い手法で不必要なのでしょうか。もちろんそのようなことはありません。自動化が進んでもそれを考えて作るのは人であり、IoTもAIも目的を達成させるための道具であるからです。自動化やIoT、AIを導入しようとすると現場からは抵抗されるケースもありますが、私は「最新技術を使って5Sをしましょう」と言うことがあります。あくまでも人間が主体であり、仕組みや道具をつくる人の考え方が基本を外していたら、非効率なものになりかねません。
自動化設備の機能(動き)の大部分に搬送や待機があり、稼働時間の中で付加価値を付けている時間がほんのわずかであるということもあり得ます。IoTの推進も目的や取得したデータの活用が視野に入っていなければ、ムダなデータをムダにため込むだけに終わる可能性もあるのです。自動化やIoT導入で一見先進の工場でも中身はムダだらけな状態にならないためにも基本理念でもある5Sについて理解をしておくことが非常に重要であると思います。
良い工場は「パッと見て」わかる
「パッと見た」ことが意外と肝なのだと前の方で書きましたが、どのようなことなのか最後に述べたいと思います。製造現場に案内されたとき全体をパッと見て何か気持ちの悪さや心地悪さを感じることがあります。最初はなんだかわかりませんでしたが、そうではない製造現場と何が違うのでしょうか。「あれ?なんかすごいぞ」と思うのは単に清掃が行き届いていることや、整然としているということなのでしょうか。
かの有名なスティーブ・ジョブズの言葉に次のようなものがあります。
デザインとは「どう見えるか」ではなく、「どう機能するか」の問題である。
デザインは見え方に凝るのではなく、その製品がどう機能するかを追求して完成されているということなのでしょう。製造現場には材料に付加価値をつけるという機能があります。価値をつけるところ、例えば加工点に集中してその他のムダなものを極力除くことできれば、美しい姿になるということなのではないでしょうか。ムダの無い機能美、それがパッと見て美しいということなのだと思います。
さらに例を挙げます。寿司職人の仕事や茶道の動きに共通することは何でしょうか。両方とも芸術性を感じる美しい動きですが、なぜそうなのでしょうか。ただ早いわけでもなく、きらびやかなわけではありません。そうです、ムダが無いのです。
ムダがないものは美しいです。ムダの無いもので思いつくものを挙げてみます。プロスポーツ選手の動き、飛行機やスポーツカーのデザインなどはいかがでしょうか、みな芸術的で美しいと思いませんか。そうです、パッと見て美しい製造現場はムダのない5Sができている機能美を感じさせてくれるのです。
5Sを突き詰めていくとそのような目が養われます。心地悪さは、通路にモノが置かれていることや加工場所なのか材料置き場なのかわからない状態、作業者が材料を待っている状態、垂直並行ではないなど、ムダが目に入ることによるものなのだと私は思います。皆さんもそのような目を養ってみませんか。
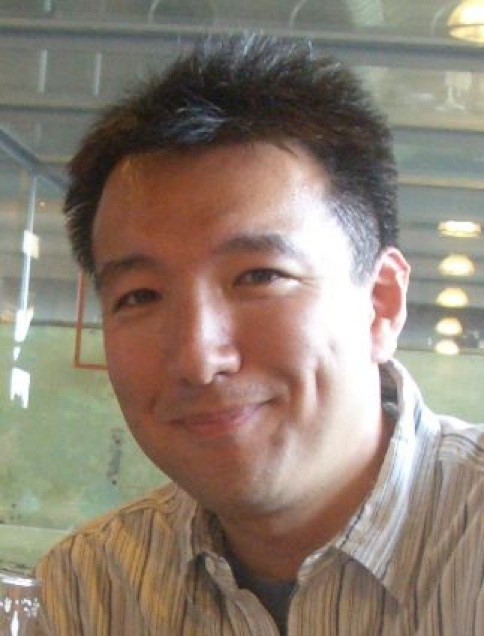
執筆者K.S氏
大学卒業後、エレクトロニクス業界の大手企業に入社し、生産技術部門勤務。
グローバル売上数千億円規模のデジタルプロダクト事業にてSCM導入とマスカスタマイゼーションを効率的に実現するPLMの活用を牽引。IT外資系企業や物流業界の企業を経て、製造業にてCDOとしてIoTや全社デジタル化を推進。