生産
IoTを活用した生産効率の改善や新規製造ラインの立上げ、既存生産ラインの革新など、実働型で支援します
今後、日本の人口減少が見込まれるなかで、特に技術・技能人材の人材確保が厳しくなることが予想されます。また、IoTをはじめとする第4次産業革命に関連し、現場のデータ収集・活用、デジタルツールの活用の重要性も増しており、日本の製造現場を取り巻く環境は複雑化しているといえます。HiPro Bizは、IoT化へのスモールスタートから大規模なシステム改革まで、製造現場の課題に対しての豊富な支援実績があります。
- このような課題はございませんか?
-
- 1工場全体の目標管理が曖昧になっており、生産目標未達の状態が続いている。
- 2工程のボトルネックを把握できておらず、材料・部品・工程の仕掛りが大量に滞留している。
- 3生産工程の自動化のためにシステムを導入したいが、社内にノウハウがない。
ものづくりの現場で遭遇する3つ問題
①見える化が出来ていない
「現状」と「あるべき姿」とのギャップに気が付いていない、あるいは誰か一人が気付いていても放置されたままになっているなど、工場全体でギャップを問題として捉え、共有する仕組みが構築されていないという事象が多く発生しています。これでは目標管理も曖昧になり、適切な速度でPDCAも回っていきません。このような状態では、生産目標が未達、という状態が恒常的になっていくと考えられます。
②各部署間のベクトルがばらばらになっている
生産性が上がらない多くの工場では、企業規模に関係なく、経営TOPの方針と部門長~担当者までの実行タスクが結びついていません。そのため、その工場の目指す姿が会社全体で共有されておらず、部門毎の個別最適はあっても、工場の全体最適には結びついていない施策が多く走っています。このような工場では、三現主義も掛け声だけになっているケースが多いです。
③ボトルネックが認識されていない(ボトルネックが放置されている)
ものづくりは複数の単位操作や、要員配置、工程間の能力差を加味しながら進めていきます。しかし、そこに機械や装置の段取り替え、条件出し、検査、測定などスループットを阻害する作業工程が介入するため、人材の頭のなかに蓄積され属人化しているような作業工程では、ボトルネックを把握することが難しくなっています。そのため、生産性の低い工場では「モノが停滞している」「材料・部品・工程の仕掛りが大量にある」「工場の中で忙しい職場と時間を持て余している職場が存在している」「必要な材料や部品が必要な時に確保できていない」などの状況になるケースがあります。
工場の生産性を上げる3つのポイント
①工場の見える化
見える化の第一歩は「現状」と「あるべき姿」とのギャップを把握することから始まります。まず、工場全体でそのギャップを問題として捉え、共有する。次にギャップに対する改善策を決め、いつまでに、どのレベルまで、誰が担当するかを決め、定期的に進捗を確認していきます。また、生産、販売・サービス、メンテナンス、修理といった様々な現場の繋がりで活動するものづくり企業においては、従来から行ってきている品質や生産性改善をもう一段ステップアップするために、ICT・IoT・AIを活用する企業も増えています。
②生産ラインの改善
トヨタ生産方式を理解している製造業の幹部、経営者は多くいらっしゃいます。トヨタ生産方式の2本柱はJITと自動化です。トヨタ生産方式を実現させるためには、生産を平準化し、不要な仕掛り在庫を持たない事が重要ですが、単純に真似をしても多くの場合は失敗してしまいます。自社にとって最適な部品在庫量、部品調達のL/T、中間仕掛りの持ち方、完成品在庫量、出荷のタイミングなど、全体像の把握をすることで初めて良好な体質の現場が実現できます。
③ボトルネックの改善
工程設計上のボトルネックと現実のラインのボトルネックがずれることはよくあります。機械装置でものづくりをする工場では、段取り替え、条件出し、検査、測定等、人が係る作業の効率でボトルネックは変化します。
そのため、問題のポイントが曖昧になり、有効な対策が打てずにいる課題が見受けられます。ものづくりの改善キーワードは4M(Man・Machine・Material/Method)と言われますが、要素毎にどこから手を付けていくのが最も効果的なのか、そのポイントを見極める事が重要と考えられ、また、装置でものづくりをする工場では、装置の保守管理が出来て初めて装置を活用したものづくりが上手くいきます。また、発生する装置トラブルに対応できる現場オペレーターの技術教育も大事なポイントになってきます。
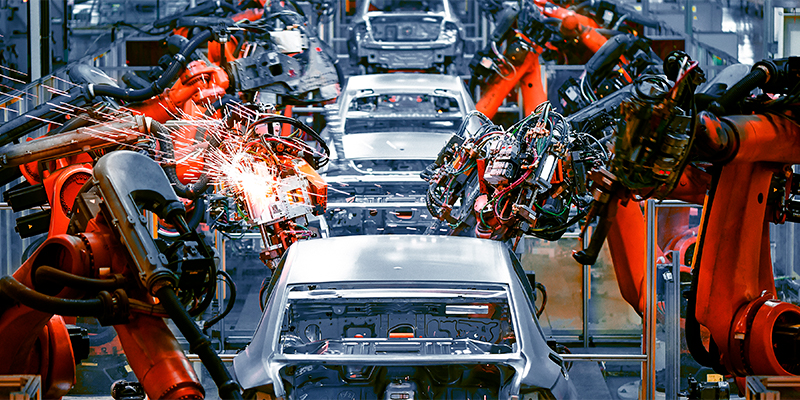
生産改善に外部の専門家のノウハウを活用するメリット
上記①~③のいずれも、技術・技能人材の確保が厳しくなることが予想される中、属人化の傾向がある作業を抽出し、関係者全員の目に見えるように形を揃えることと、自動化できない育成部分作業のによって成果につながっています。
現場が主体となって生産改善を実行し効果的に定着させるためには、生産改善に関して多くの知見を持つ専門家を外部から招き、その専門家に自社を見てもらい、自社の課題や文化、規模に最も適した仕組みを構築することが有効です。
例えばIoTを導入する際に生じやすい、システム開発側と現場との間で軋轢やジレンマの回避にも、経験に裏打ちされた中立かつ俯瞰的な専門家のノウハウやアドバイスは重要な意味を持ちます。しかし、生産改善の専門家を外部から招く手段として、採用するには難易度は高く、まずはスモールスタートからという模索に対する人件費としては、高額となります。
そこで、最もスピーディーに自社の課題を解決する方法として、HiPro Bizが提供するコンサルティングサービス(業務委託準委任契約)にて、生産改善の専門家を社内に招くことがオススメです。
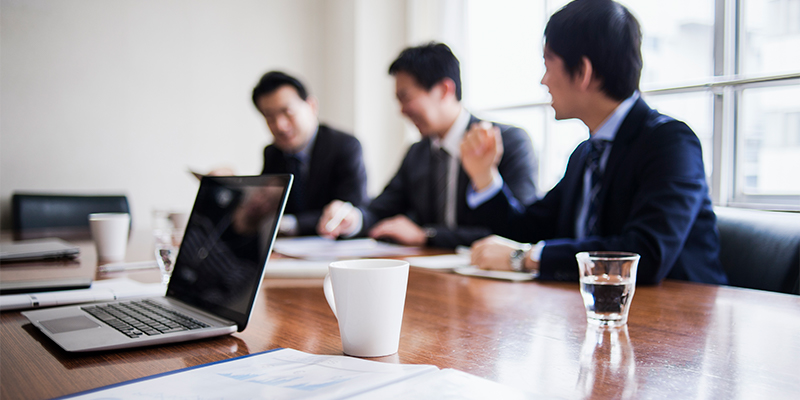
生産の
ご支援ケース
-
CASE 1
IoT×生産工場
- 業界
- 住宅設備業界
IoTを活用し、主要工場の生産効率を大幅に向上
IoTを活用し、自社工場の生産効率を上げていきたいと考えていたが、自社内に知見・ノウハウがなかった。
そこで生産×IoT分野の専門家を活用し、一部のラインからのスモールスタートを実現。現在は複数ラインのIoT化が進んでいる。 -
CASE 2
生産現場社員の意識向上
- 業界
- 建材業界
生産現場社員の意識を改善させ、生産効率を改善
自社工場の生産効率著しく悪化しており、社員の意識や生産方式の改革が必要であったが、ノウハウが無く改革が止まっていた。生産改善のスペシャリストを迎え、意識改革と新たな生産方法を定着させ、生産革新を実現した。